Fit Testing is an industry practice to ensure that a respirator fits well to a wearer, aiming to achieve a good facial seal and protection.
Typically, a fit test is done in a controlled environment with scientific test equipment while performing a predefined test protocol, and it can effectively reveal how the respirator fits at the time of testing.
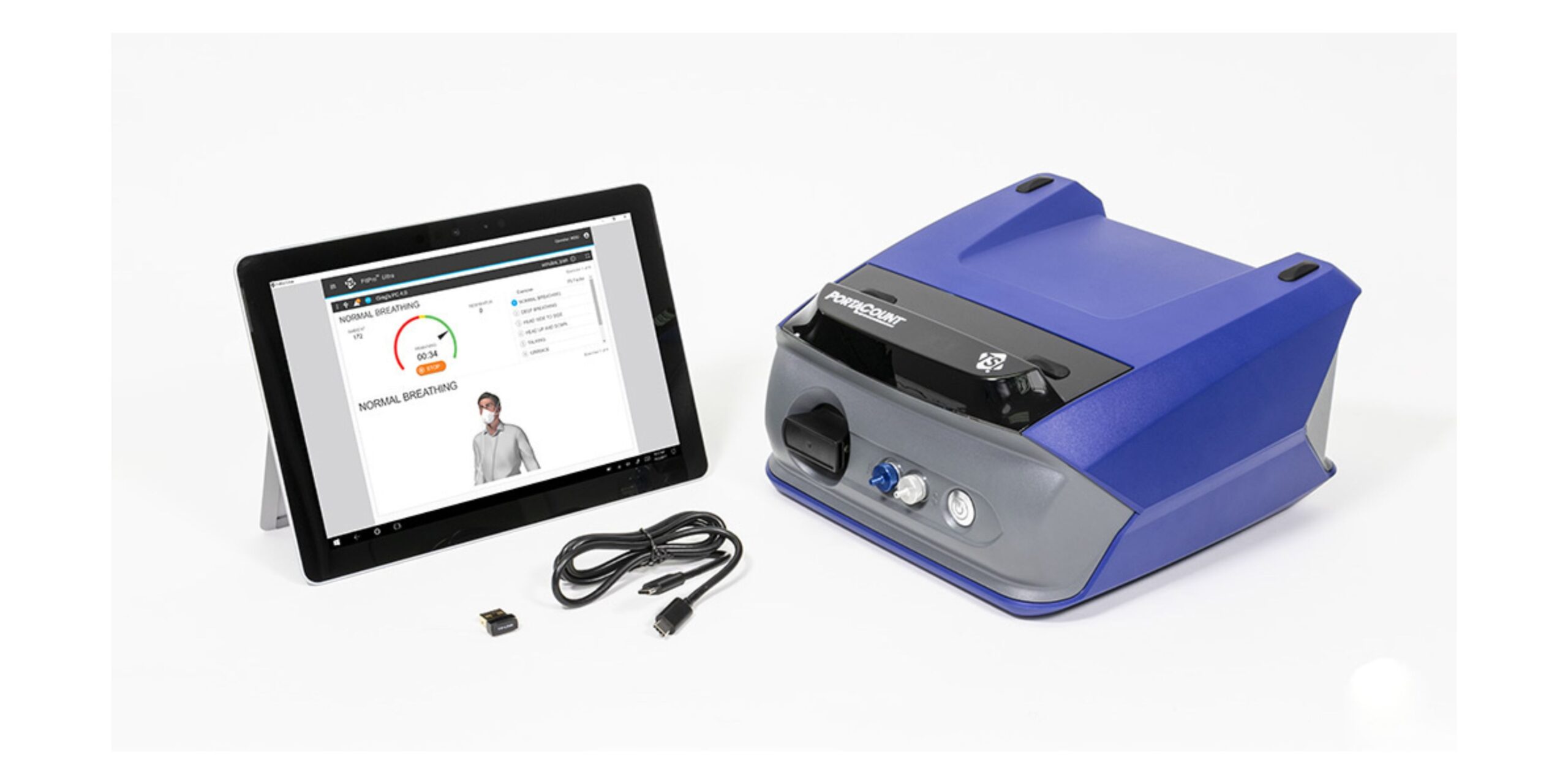
However, the real world of industrial work can be very different from and harsher than a short moment in a comfortable office, thinking about the following scenarios:
- While doing tunnelling work, formwork in high-rise buildings, crawling under a roof, workers need to focus on the tough work itself or danger around them other than minding the fit of a respirator, which is prone to shift on the face in these works, compromising the fit.
- Tasks associated with frequent moving around, high exertion, and sweating while using tools involving both hands can not ensure a good fit of the respirator once it shifts on the face.
- For young male workers, even if they are clean-shaven in the morning, they may grow stubble enough to break a good seal, making a properly fit-tested respirator leak.
Having said that, fit testing has its unique place in controlling the effectiveness of respirators.
Compliance-wise, fit testing is a necessary industry practice, it ensures the respirator properly seals to the worker’s face under controlled conditions, verifying that the selected model and size provide adequate protection.
Fit Testing can also reveal respirator system leaks or Total Inward Leakage (TIL).
We need solutions to balance regulatory requirements or intent with practical considerations.
Possible solutions:
- Engineering controls (e.g., reducing airborne hazards).
- Using respirators that are less prone to dislodging, like a full-face mask versus a half-mask.
- Using a suitable PAPR which does not rely on a tight seal to work, such as a loose-fitting PAPR.
In most cases, a suitable PAPR is your best option to ensure good protection if you have been using non-powered respirators.
However, traditional PAPRs have the following practical issues:
- Poor wearability and mobility associated with long hose waist-mount type, top-heavy helmet-mount type, and front-heavy face-mount type.
- Difficult to clean and maintain.
- Prohibiting high costs.
The great news is that, Aimwell® AYO™ WX series around-neck PAPRs have dramatically improved all these problems.
The series comprises a selection of low-profile half-face and full-face mask assemblies and a selection of easily detachable powered units worn around the neck, available in both tight-fitting and loose-fitting configurations, no hose, no belt, no hassles.
Certified by CMI ProdCert, this award-winning PAPR series offers the highest-in-class protection (PAPR P3), breakthrough mobility and flexibility, ease of use and maintenance, with exceptional value for money.